Challenge
A global manufacturer of electric mining shovels required a reliable performing motor for their dipper system. Mining shovel owners and manufacturers require a dipper trip control system that works consistently with low maintenance.
Application requirements:
- High peak torque, extreme duty cycles and operation in critical environments
- Explosion proof, UL & ATEX required
- Efficient and energy sound solutions include power density and thermal management
- Flexibility for custom application solutions i.e., mounting flexibility, custom flanges, holding brake, etc.
- Fast response across speed range
POWERTEC Solution
POWERTEC PACTORQ® Brushless Motors Features & Specifications
- Optimized magnetic design
- Neodymium, Samarium and Ferrite magnets
- Long life bearings with grease
- NEMA enclosures with metric mounting options
- Rugged IGBT class “H” insulation system and rated for class “F” temperature rise
- Flexible design incorporates many options
- UL recognized, CE (Conformity European)
- Meets IEC requirements
- Designed, double finned aluminum frame
- Temperature range of -40°C to +160°C
Benefits
- Compact power dense design for installations with limited space availability without compromising performance
- Virtually zero losses due to rotor induction currents, reducing energy use and cost
- Accurate speed and torque control, no losses due to slip
- Longer service life: reduced maintenance time results in
cost savings and less downtime
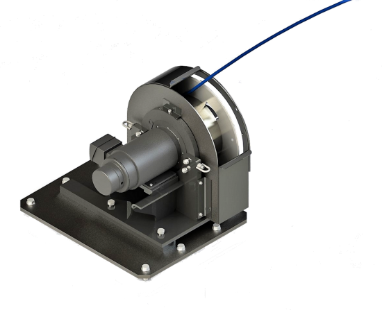
RESULTS
POWERTEC has been supplying these motors to the manufacturer for more than a decade with benefits:
- Reduced cycle time with reliable door trips.
- More loaded haul trucks per shift help lower cost per ton for the shovel owners.
- Mining shovels with POWERTEC motors help provide a reliable trip and slack take up operation.
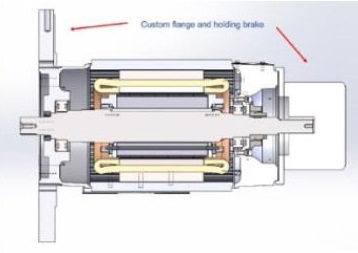